System Description
In cereal or chocolate bars production, Slitters are used to cut slabs made from cereal masses with sugar or chocolate wafers; the slitter consists of circular knives mounted on a rotating shaft.
Downstream of the slitting system, the spreading system is located; Spreaders are used to spread sticky products or to prepare products prior to the chocolate enrobing process; the spreading system consists of spread individual belts mounted on toothed sleeves fixed at rotating shafts.
Downstream of the slitting system, the spreading system is located; Spreaders are used to spread sticky products or to prepare products prior to the chocolate enrobing process; the spreading system consists of spread individual belts mounted on toothed sleeves fixed at rotating shafts.
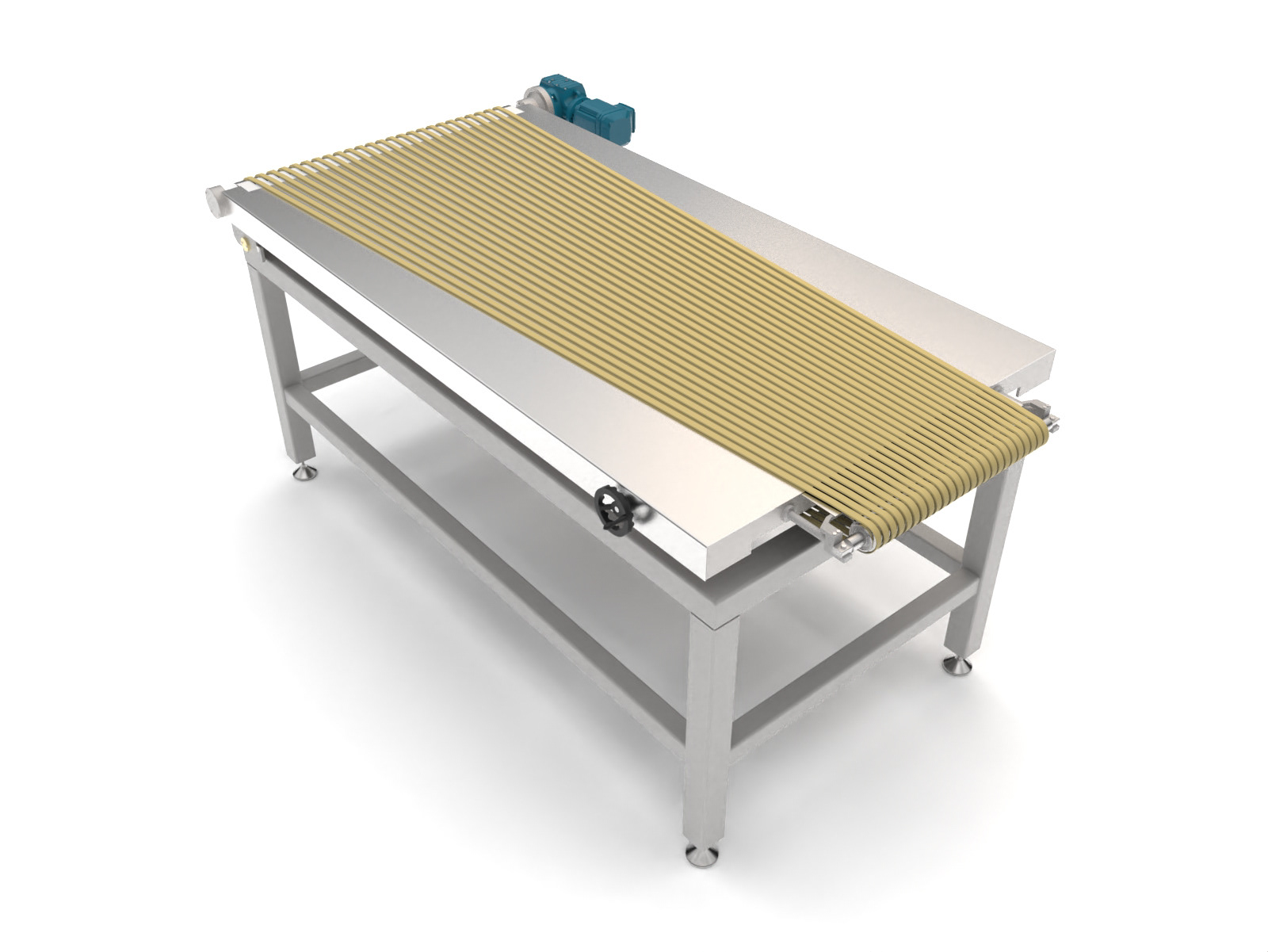
Spreading System - Overview 1
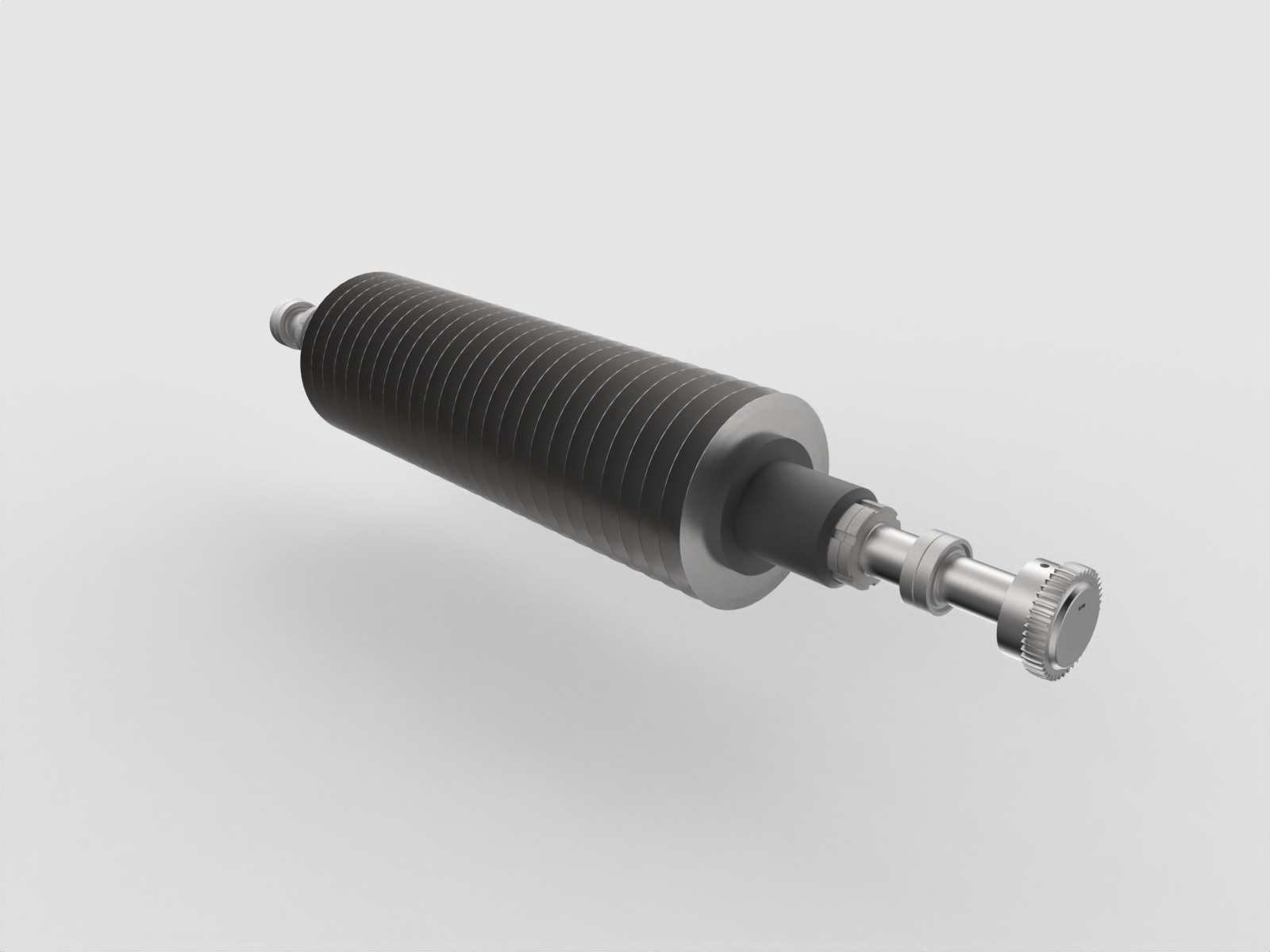
Slitting System - Overview
Project Objectives
The customer is an FMCG manufacturer of breakfast cereals & cereal bars and owner of a cereal & chocolate bars production line.
The main customer's objective is to produce bars in different dimensions to the standards of the existing production line, therefore another set of spreading and slitting systems is needed with customized dimensions and features unavailable at the OEM.
Hence, there was a need to locally reproduce and manufacture the new set of spreading and slitting systems as part of a reverse engineering project involving 3D modeling, assembling, material selection and manufacturing.
Design Process
The reverse engineering process started by measuring every detail in the existing systems and then reproducing them in 3D modeling & assembling using SOLIDWORKS. The first stage is a draft modeling & assembling for basic parts, while in the second stage, drawings, 3D models and assembled systems were customized following customer's requirements.
Some of the design features are improvised especially regarding the techniques of holding the bearings in place by introducing inner edges to the sleeves and external retainers (circlips).
Major customization of the systems involved modifying the dimensions, numbers and spacing of the sleeves' teeth, shafts lengths, groove cleaners spacing and numbers, base structure dimensions and knives and spacers distribution.
Materials used in the spreading system are food grade stainless steel 316 & stainless steel 304 and polyethylene (belts).
Materials used in the slitting system are food grade stainless steel 316 & stainless steel 304 and food grade S136 mold steel (bushings & spacers).
Market available used components are:
1. Manual gearboxes and couplings for the manual tensioning system of the spreading belts.
2. Rotating wheel for the manual tensioning system of the spreading belts.
3. Geared motor drive for the spreading system.
4. Circular knives.
5. Slitter's bushings and spacers.
6. Slitter's coupling hub.
7. Bearings.
8. Structural members for the base structure.
9. Circlips and fasteners.
1. Manual gearboxes and couplings for the manual tensioning system of the spreading belts.
2. Rotating wheel for the manual tensioning system of the spreading belts.
3. Geared motor drive for the spreading system.
4. Circular knives.
5. Slitter's bushings and spacers.
6. Slitter's coupling hub.
7. Bearings.
8. Structural members for the base structure.
9. Circlips and fasteners.
3D Modeling: all parts in the assemblies were modeled using SOLIDWORKS except for geared motor drives, slitter's coupling hub and bearings; they were acquired from readily available online 3D models.

Spreading System - Overview 2
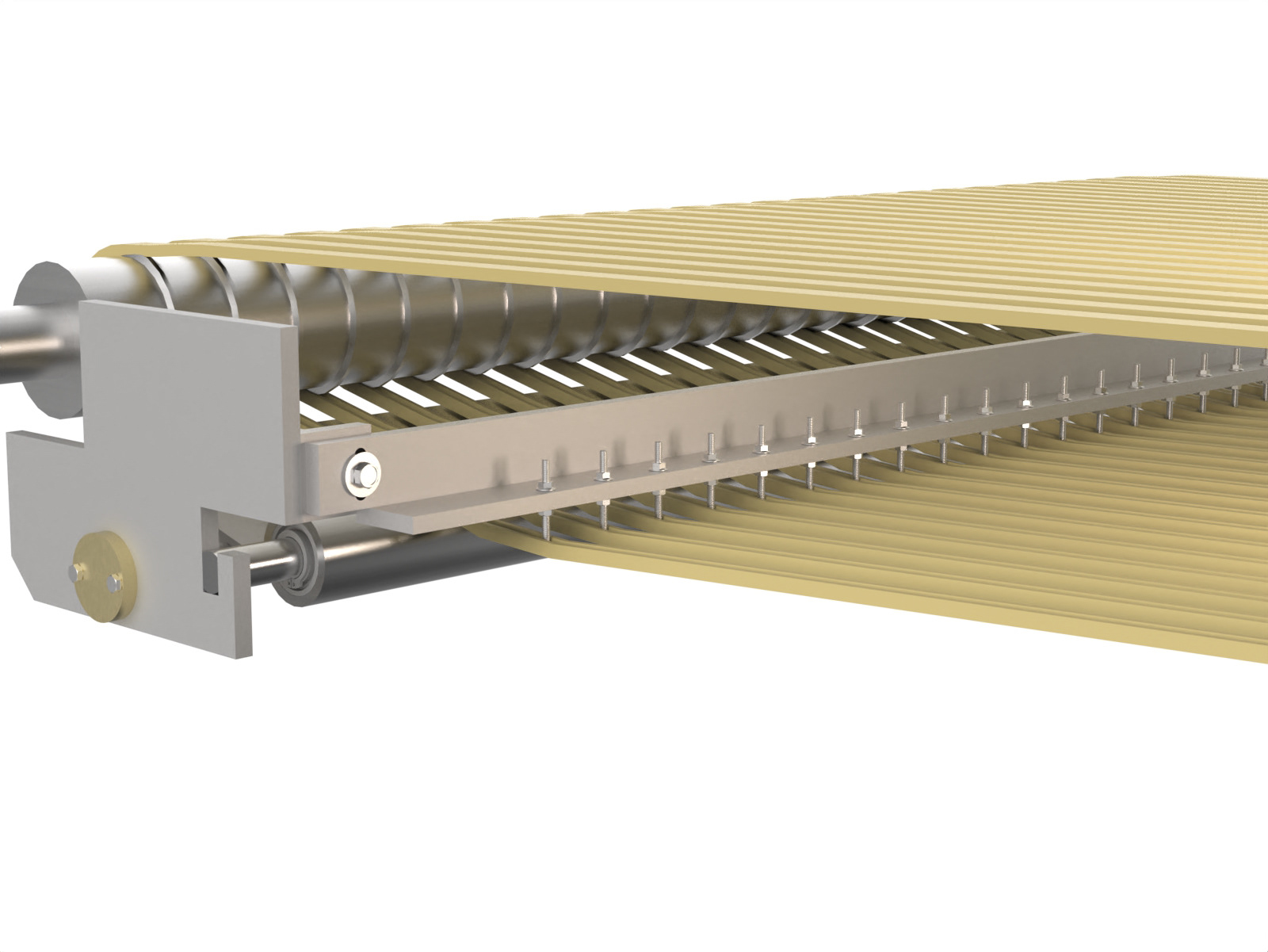
Spreading System - DE Shaft Side with Groove Cleaning Device & Tensioning Roll
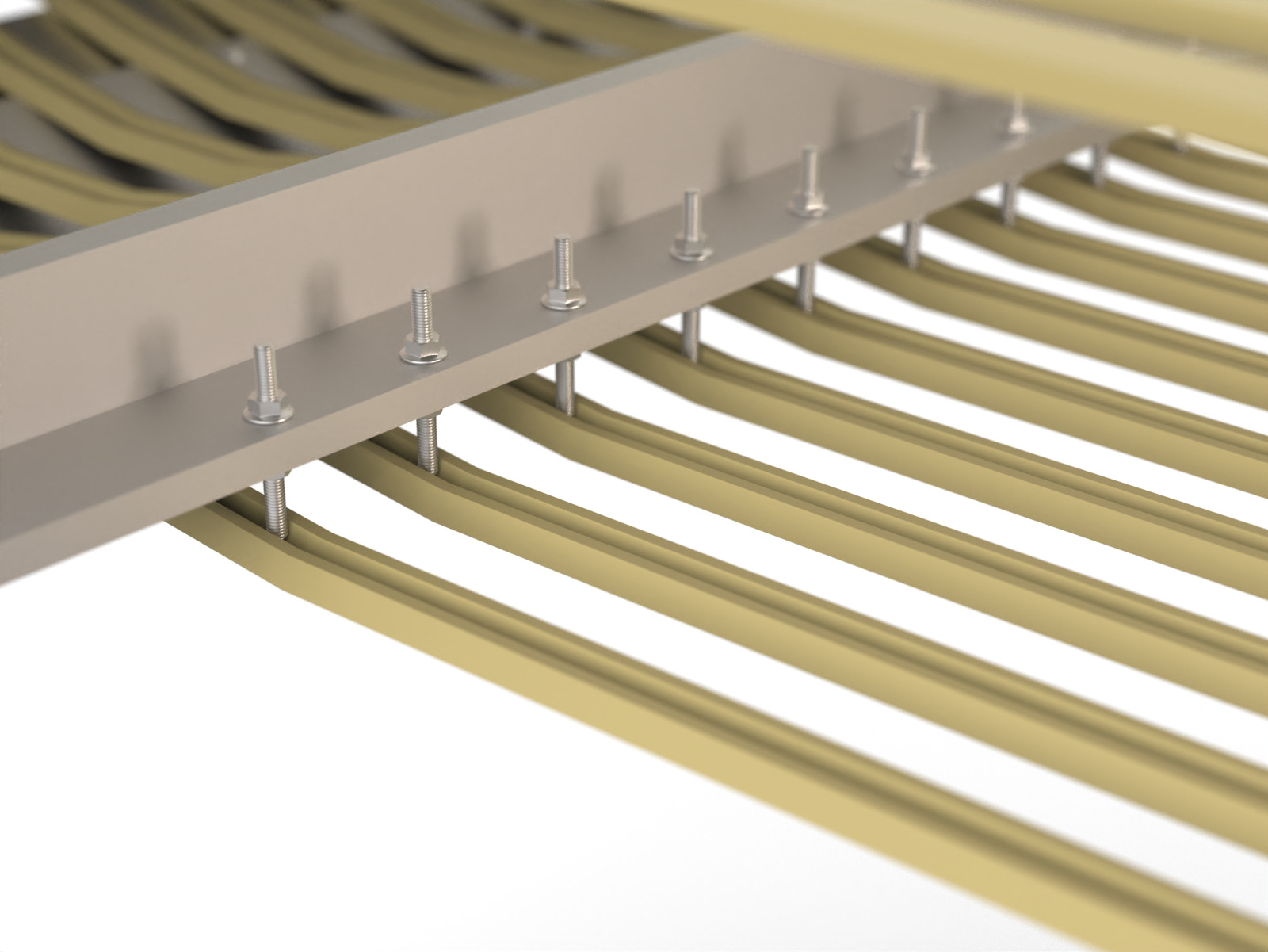
Spreading System - Belts' Grooves' Cleaning Device
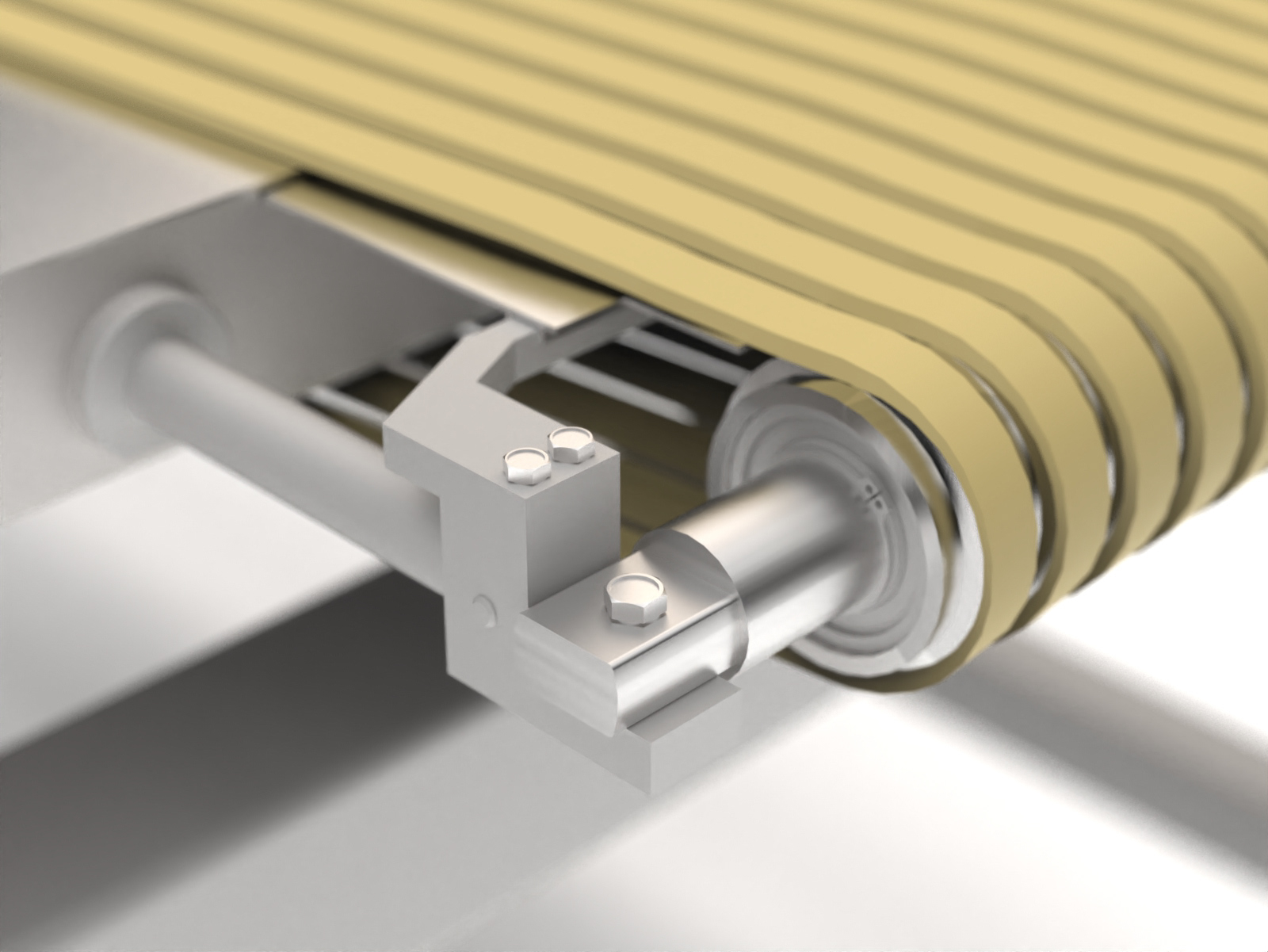
Spreading System - NDE Shaft
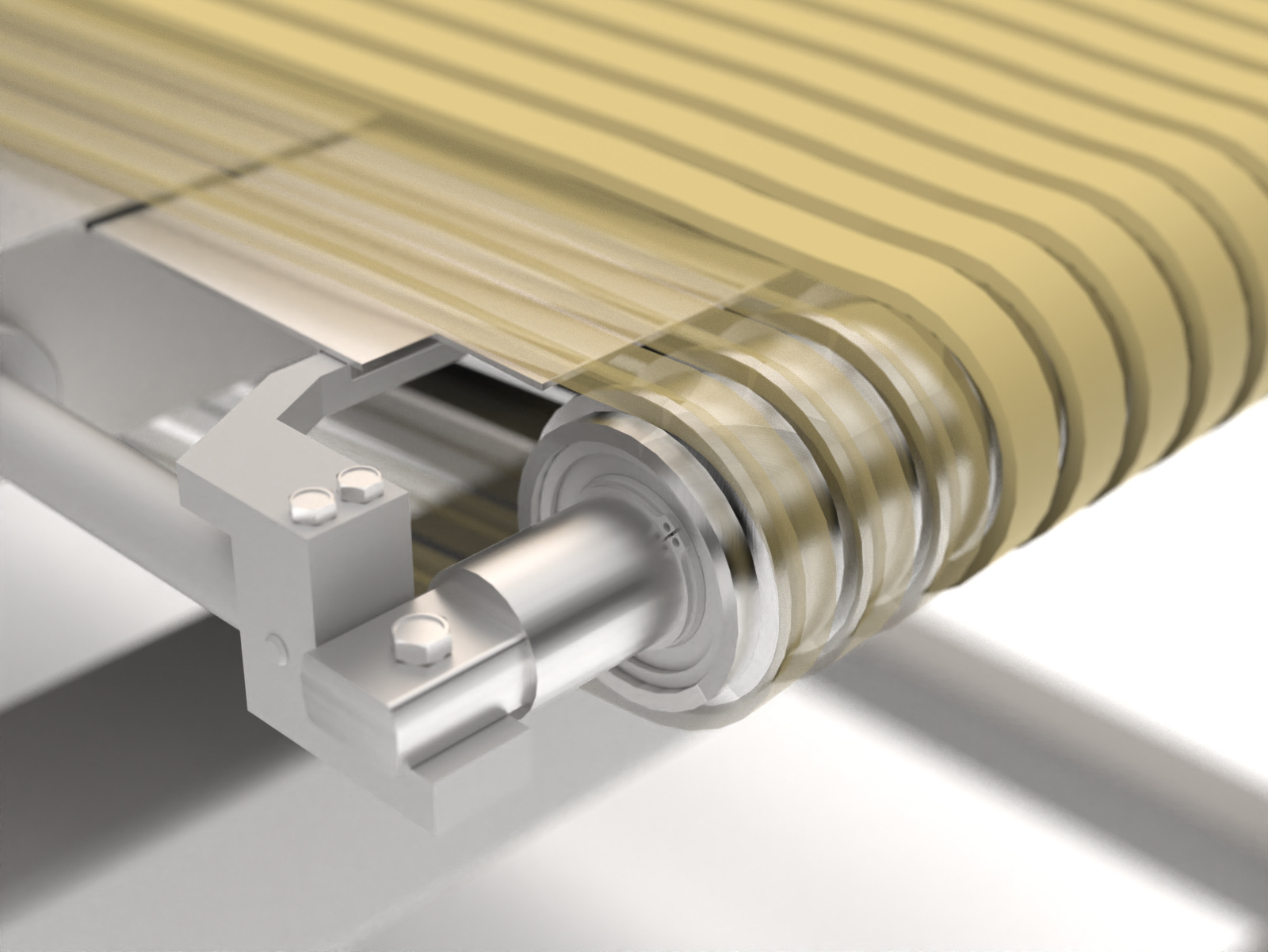
Spreading System - Belts Mounting Details
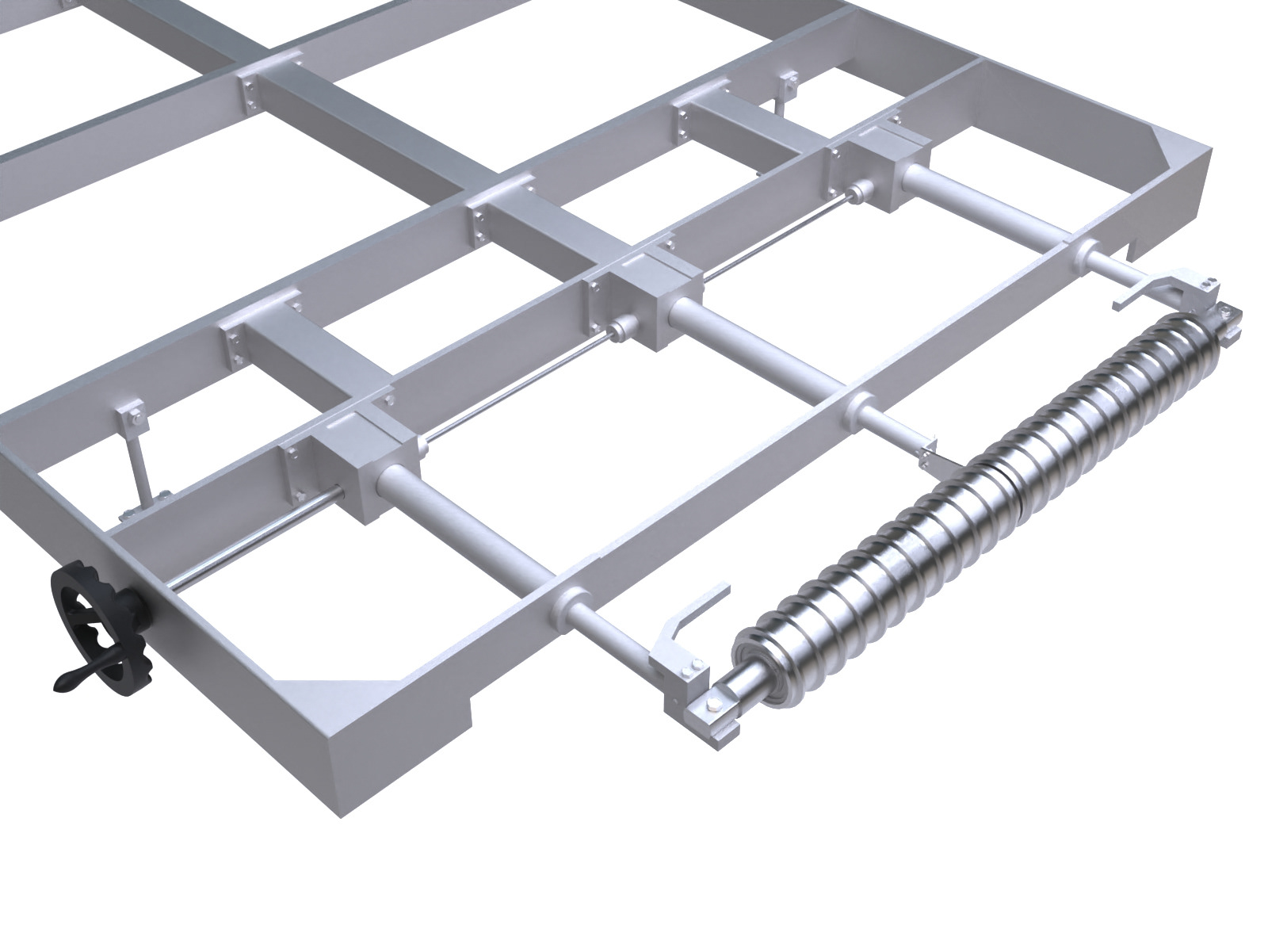
Spreading System - Base Structure with Manual Belts Tensioning Mechanism
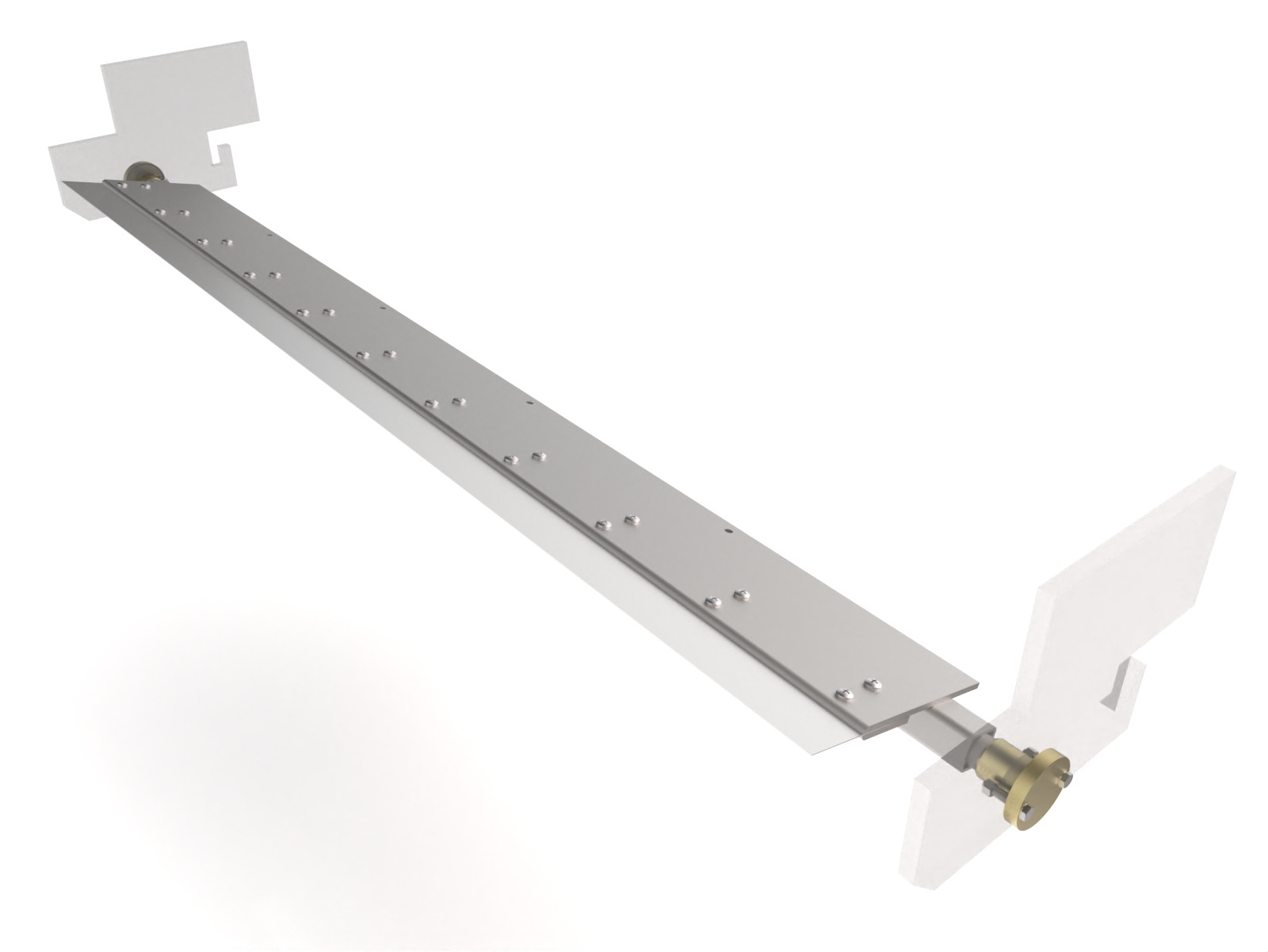
Spreading System - Belts Scraping Device
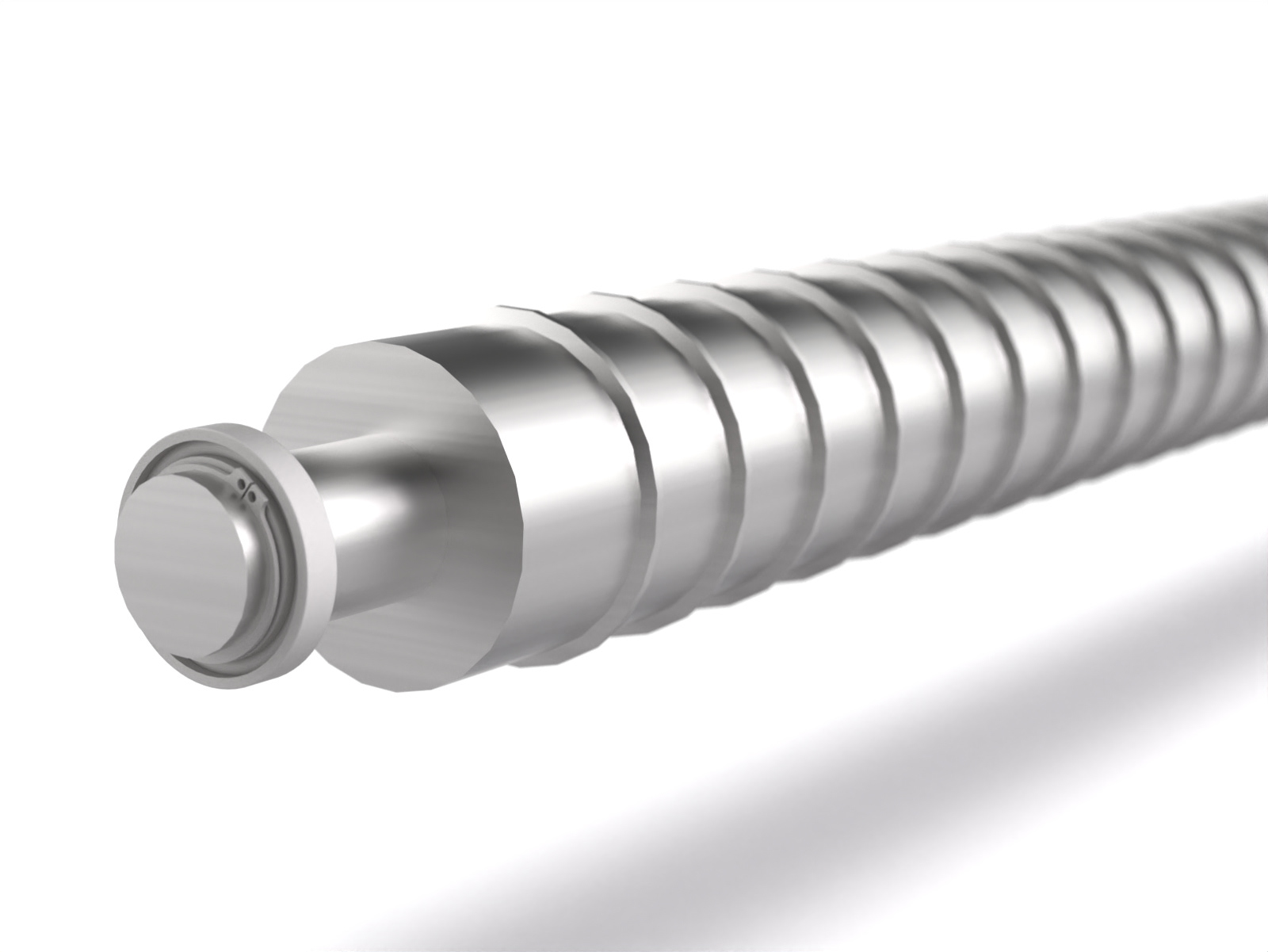
Spreading System - DE Shaft with NDE Side's Bearing & Retainer
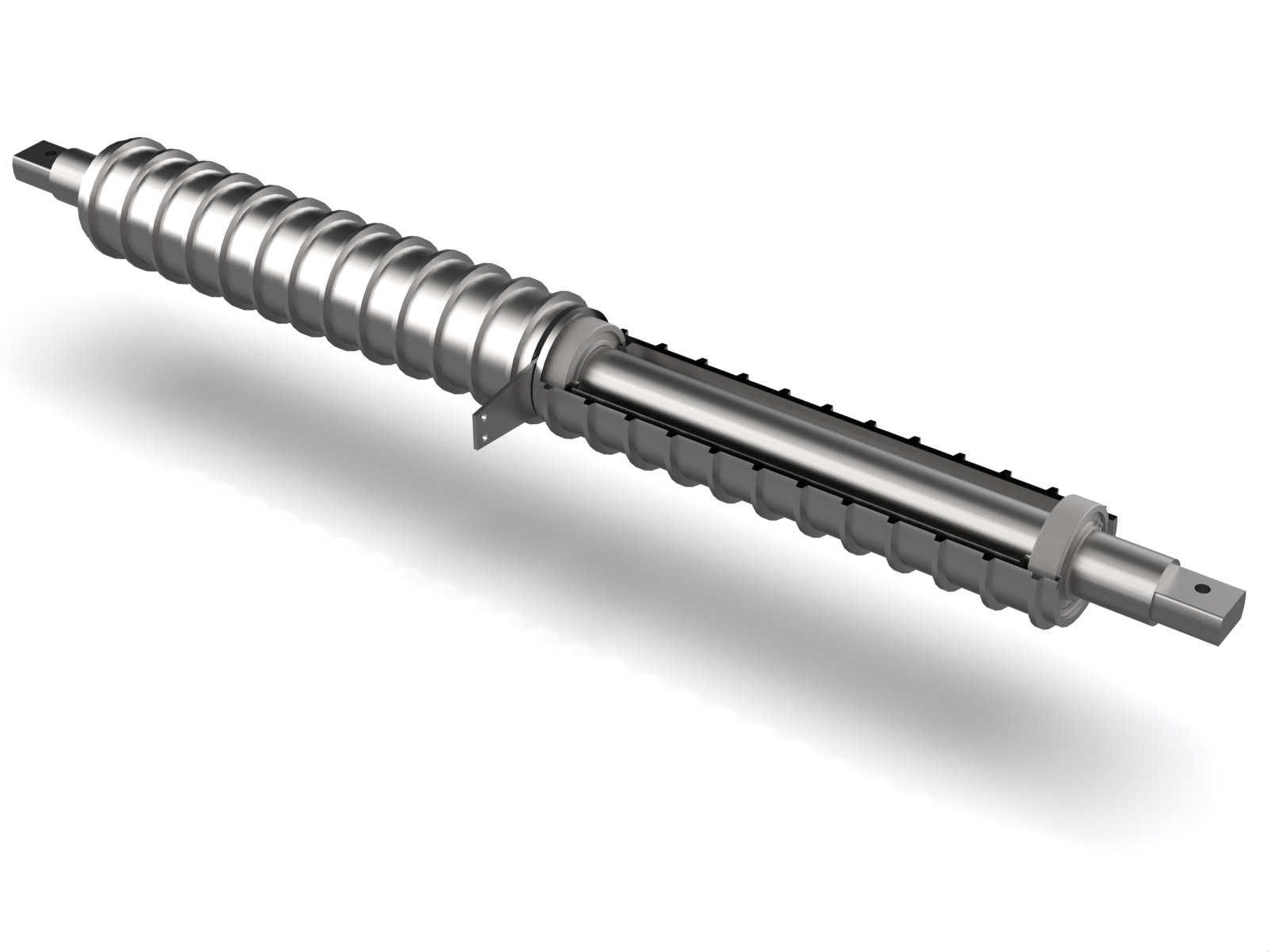
Spreading System - NDE Shaft Cutaway View - Bearings Inside Sleeves
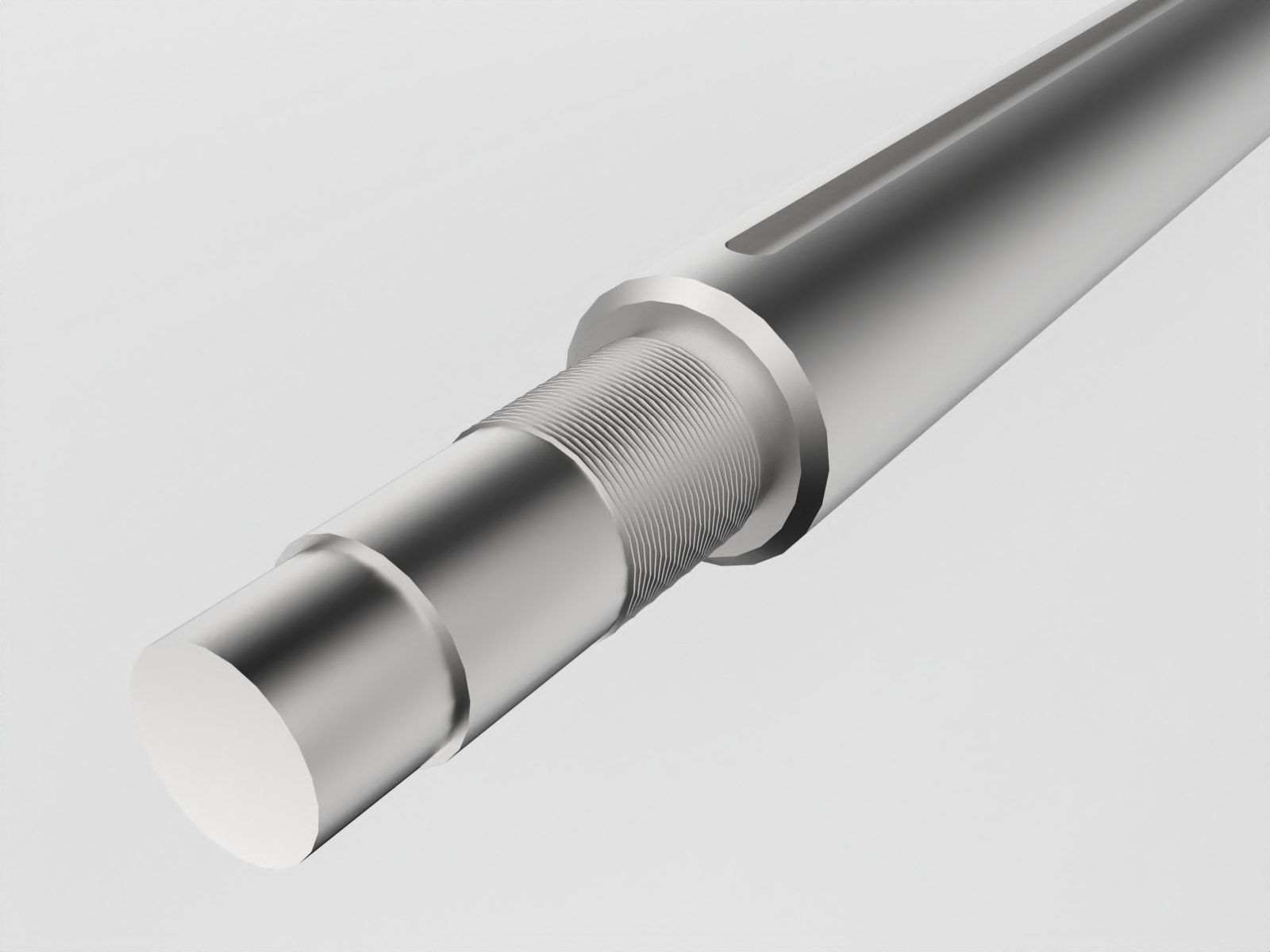
Slitting System - Shaft Body - NDE Side
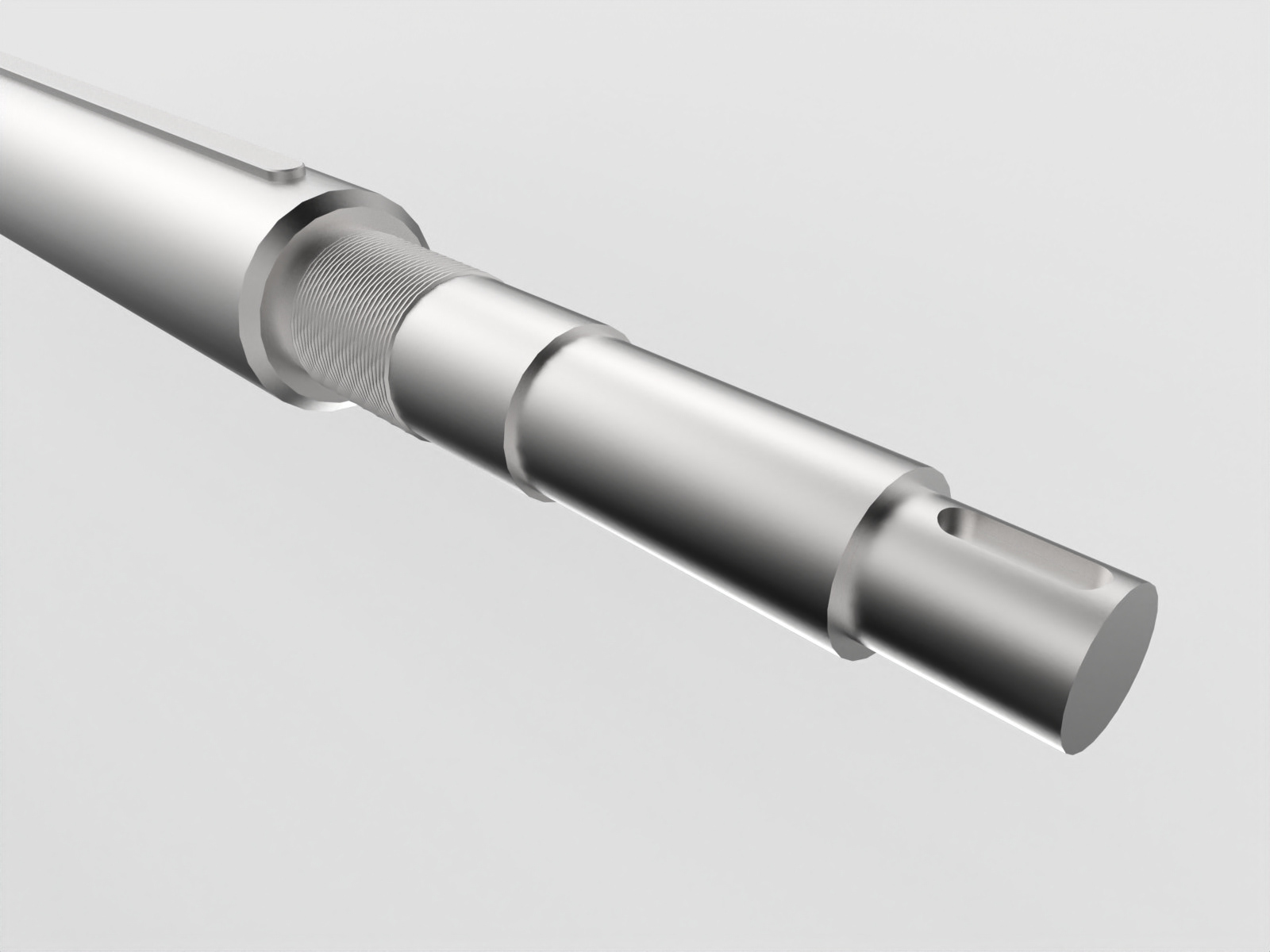
Slitting System - DE Side
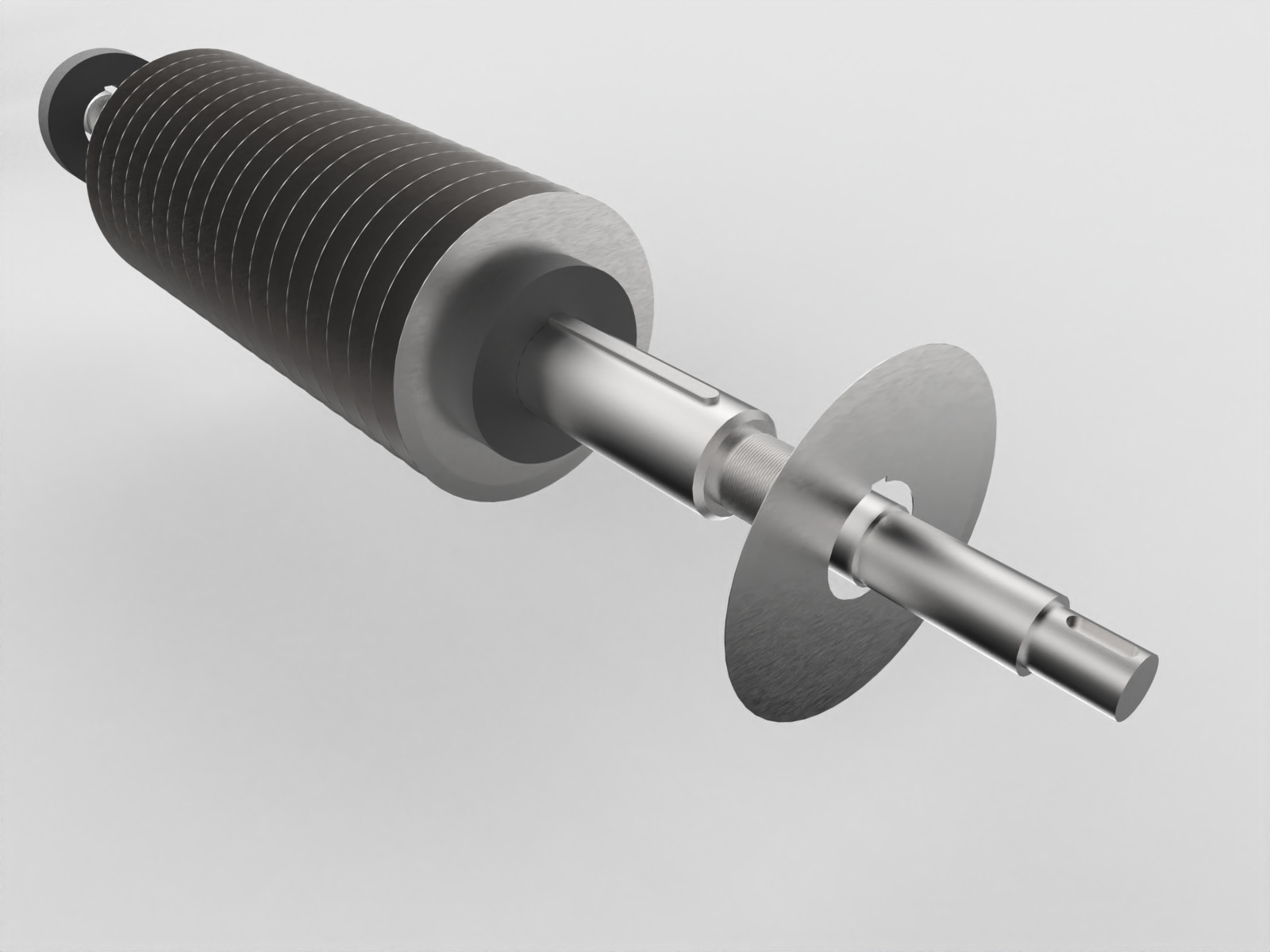
Slitting System - Knives & Spacers Installation

Slitting System - Round Nuts, Bearings & Key (DE Side)
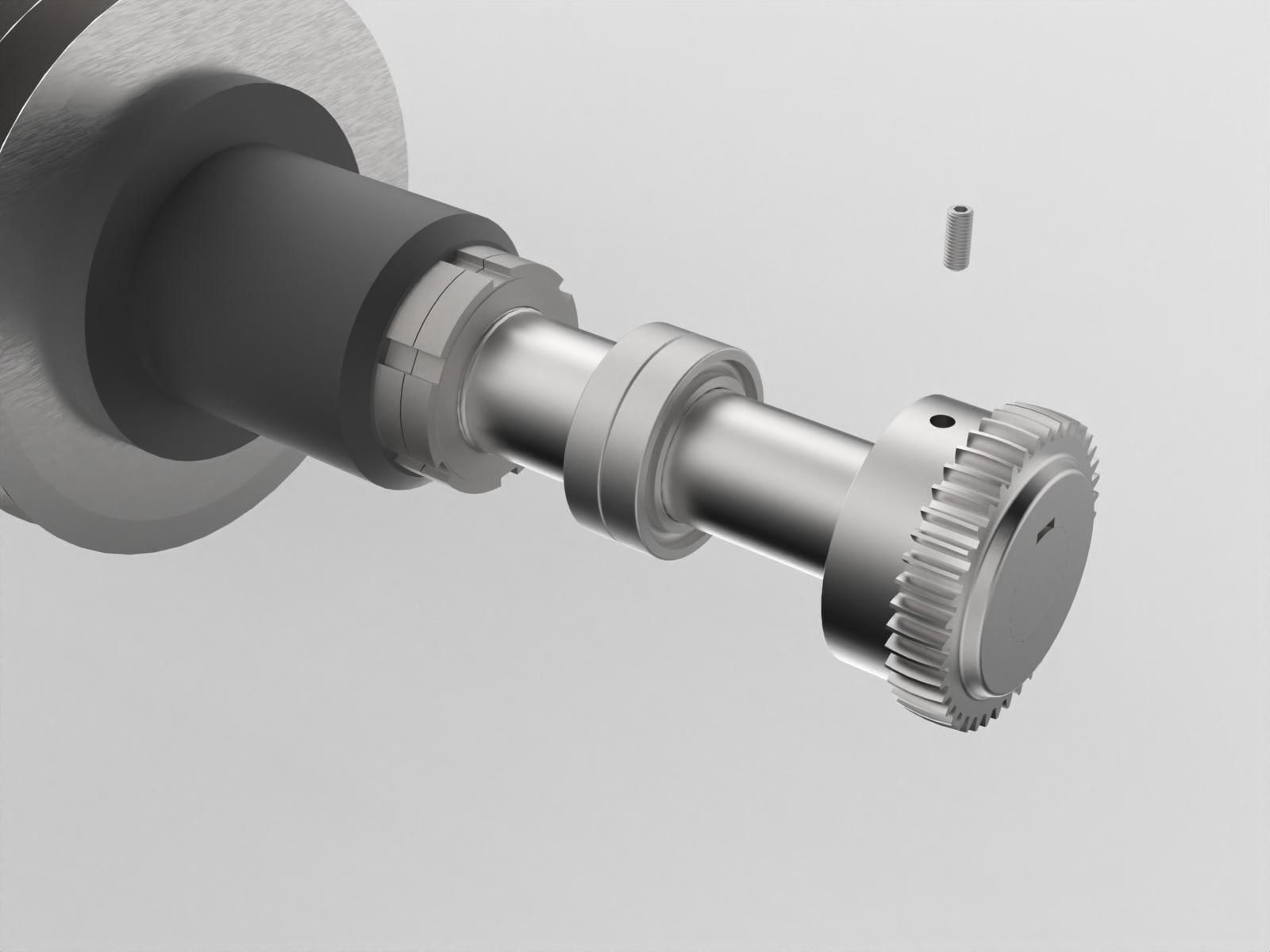
Slitting System - Coupling Hub Installation
Slitting System - Components Installation
Important Notice
The original design is a property of the original equipment manufacturer (OEM). There is no intention behind this project to commercially produce or sell the products or the designs.
All published drawings, renders and animations are properties of owners, developers or OEM and were published for professional record only.
Design files or renders shall not be distributed or used under any circumstances.
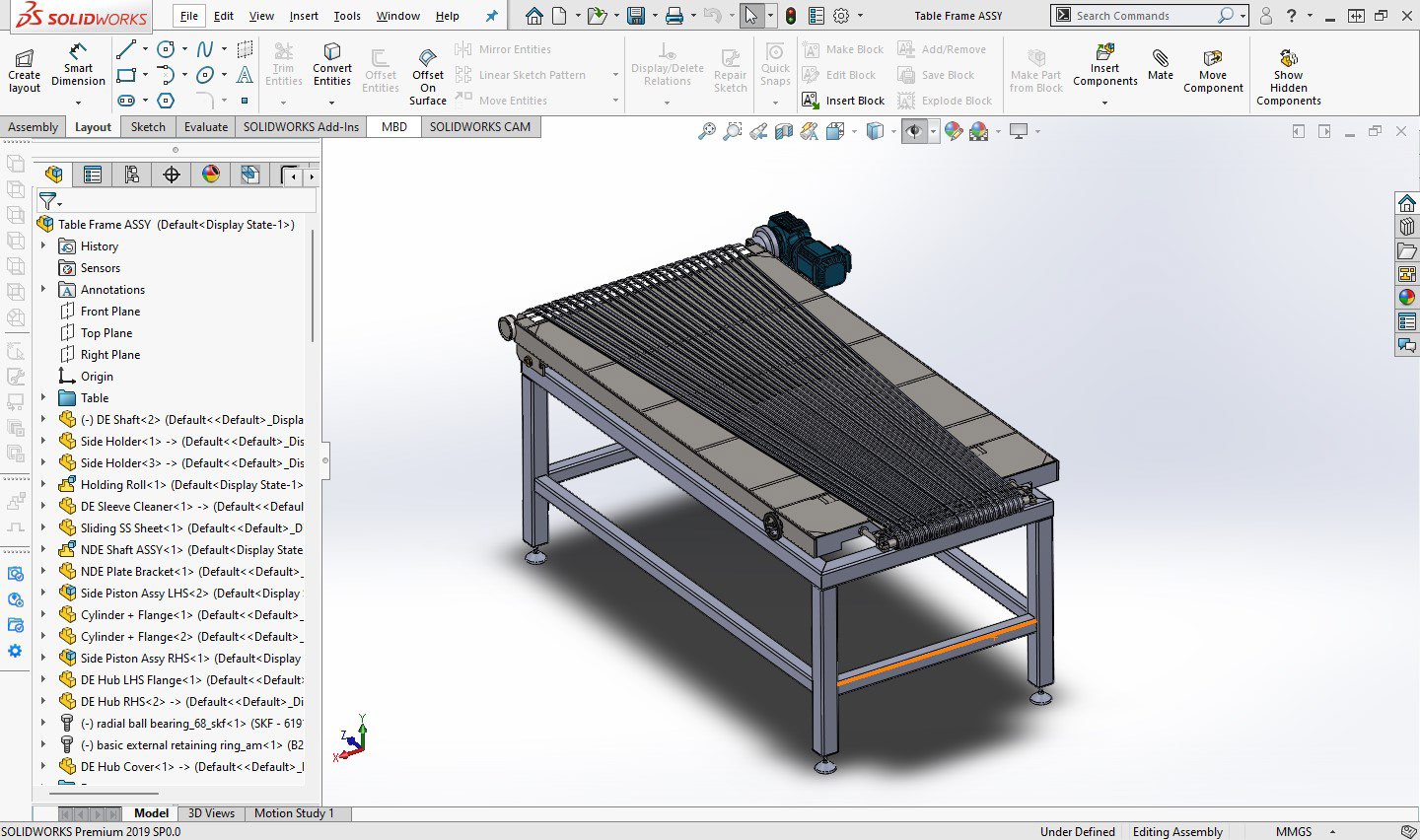
Spreading System - SOLIDWORKS Overview
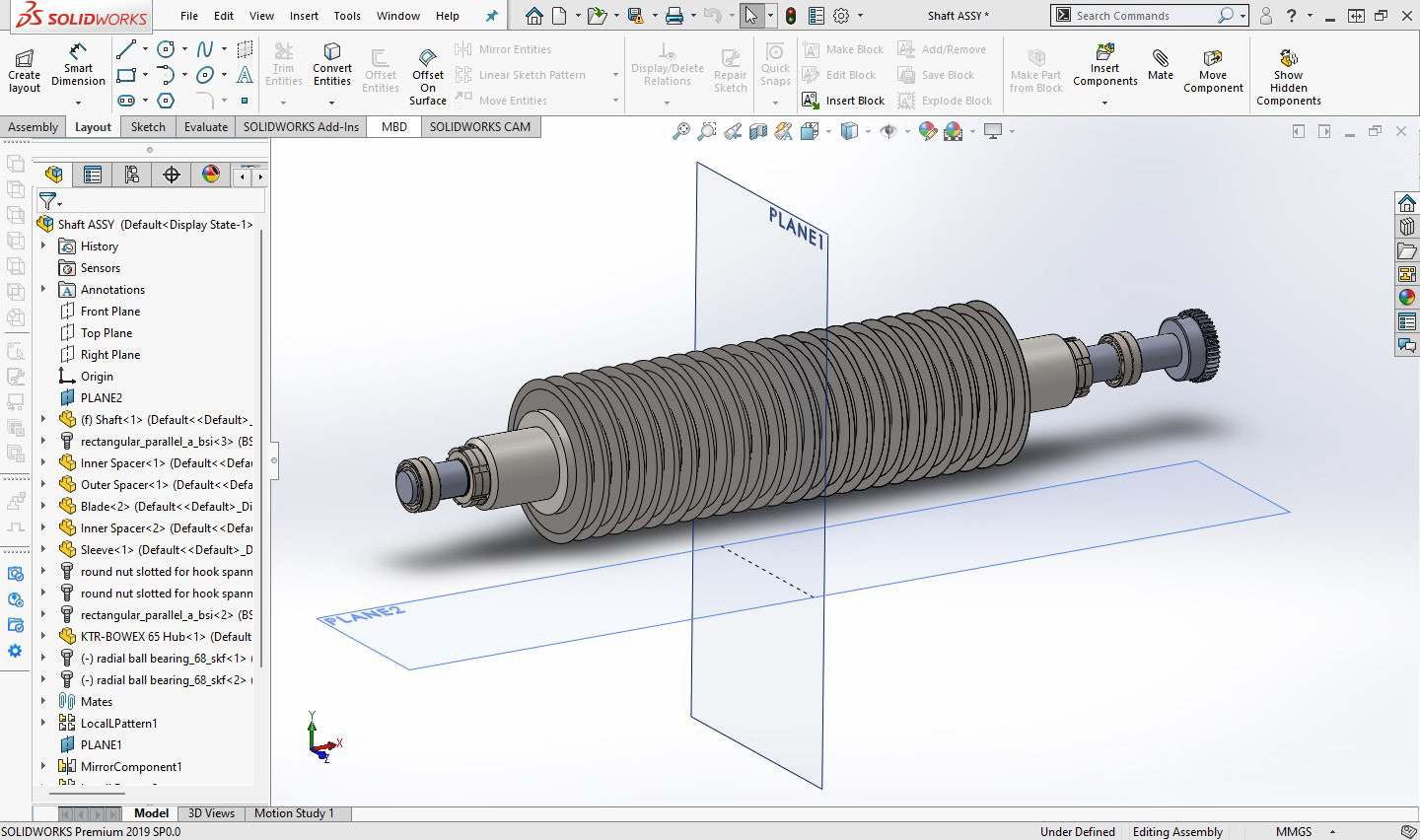